on le surnomme "l'acier vert" de part ses qualités physiques, mécaniques, et la ressource qu'il représente.
Ce matériau, exotique et plutôt insolite voici quelques années, a pris place dorénavant dans notre habitat quoditien, que ce soit dans nos cuisines, sur nos sols, dans le mobilier.
Pour les bateaux, son entrée se fait plus timidement. Sorti des quelques mains-courantes en vente dans les magasins d'accastillage et une utilisation en vaigrage par certain nombre de plaisanciers, le bambou reste pour l'instant très anecdotique.
Ce matériau pourrait cependant conquerir le domaine nautique dans les années à venir et ce serait plutôt bénéfique au regard de ses nombreux avantages et qualités.
Son utilisation pour la fabrication de mâts commence à poindre,
cf Fabrication d'un mât en composite bambou/carbone
il me semble qu'il pourrait avoir tout son intérêt pour la réalisation des nervures d'une aile souple, avec des lamelles brutes de bambou pour les parties droites et du lamellé-collé pour les parties courbes.
cf Le bambou pour les nervures
Le texte qui suit est extrait d'une étude, intitulée "Etude, réalisation et analyse de poutres lamellé-collé en bambou", réalisée par Benoît Hargot, dans le cadre de son parcours au sein de l'école d'ingénieurs bruxelloise, l'ECAM.
Généralité
Le mot « bambou » provient du malais "mambu" qui signifie "bois indispensable".
Le bambou appartient à la famille des graminées à savoir des Poacées (tels le blé, le riz, le maïs), sous-famille des Bambusoidées. Cette sous-famille regroupe entre 1100 et 1500 espèces réparties entre 60 et 90 genres de bambous différents.
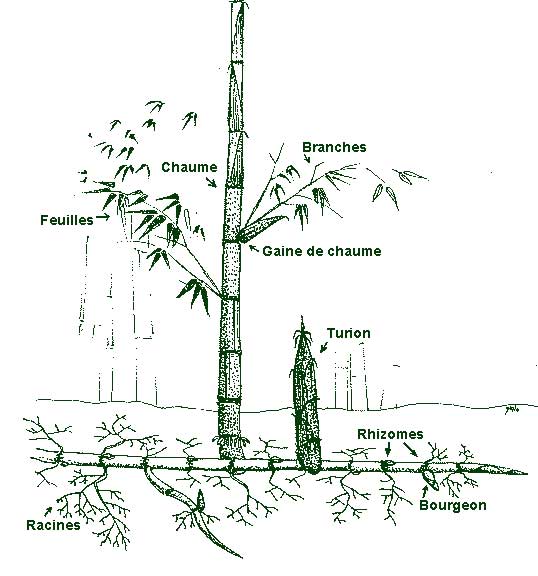
Figure 1 : Les différentes parties du bambou
Le rhizome est le système racinaire qui détient les réserves nécessaires à la croissance de la plante. On distingue deux sortes de propagation : la sympodial et la monopodial. La première forme une touffe plus ou moins dense de rhizomes courts et épais. La deuxième, dite traçante, génère des rhizomes longs et minces.
Autour des nœuds du rhizome se développent les racines et bourgeons. Certains bourgeons vont se développer et sortir de terre sous forme de turions enveloppés par une gaine protectrice. En se développant, ils forment des chaumes (cannes), généralement creux et constitués de nœuds et d’entrenœuds. Cette alternance constitue différents caissons au moyen de diaphragmes (fig. 3).
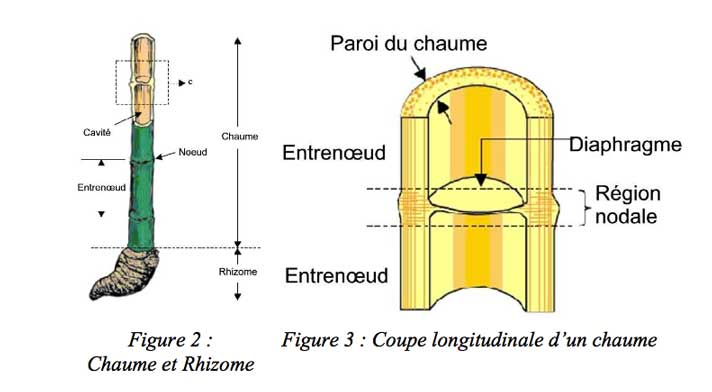
Observons les lignes verticales dans la paroi qui représentent les fibres (fig. 3). Elles sont déterminantes au niveau des propriétés mécaniques du bambou.
Certaines espèces ont un chaume pouvant atteindre 35 m de haut et un diamètre de 25 à 35 cm. D’autres ne dépassent pas le mètre (en hauteur) et le centimètre (en diamètre). Contrairement aux troncs d’arbres se développant sur leur diamètre, le chaume se déplie comme une canne télescopique, à un rythme qui varie selon les espèces et conditions de croissance (jusqu’à un mètre par jour). Il atteint ainsi ses dimensions définitives en une saison.
La floraison reste le phénomène le plus mystérieux des bambous. Elle se produit à des intervalles de temps très longs et irréguliers, souvent de manière synchronique dans le monde entier pour une espèce bien définie, et cela, indépendamment de l’âge de la plante. Après avoir fleuri, les chaumes se dessèchent et meurent.
Le bambou se développe spontanément en Afrique, en Océanie, davantage encore en Asie et en Amérique. Il s’est adapté à de nombreux climats et températures (jusqu’à -20°). On le retrouve dans des écosystèmes très divers, également à des altitudes extrêmes (jusqu'à 3000 m dans l'Himalaya).
Ces qualités écologiques sont un formidable atout pour répondre aux actuels défis environnementaux : croissance rapide, rendement à l’hectare de plus du double de ceux connus pour le bois (jusqu’à 20-30 [T/(ha.an)]), alternative aux bois exotiques (déforestation), grande résistance à la sécheresse et à la pollution, assainissement des sols et épuration des eaux usées, un système racinaire à rhizomes empêchant l'érosion des sols, haut rendement photosynthétique, assimilation des carbones et production d’oxygène, formation de bosquets et de reboisements attirant diverses espèces d'oiseaux et d'animaux, source alimentaire (pousses souvent comestibles), etc.
La consommation énergétique nécessaire à la production rapportée à l’unité de résistance du matériau nous montre encore un avantage écologique loin d’être négligeable en faveur de l’utilisation du bambou (tab.1).
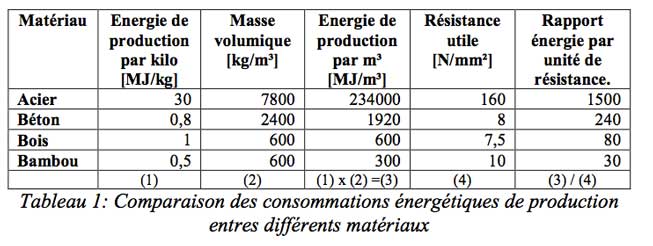
Il faut néanmoins rester prudent avec les valeurs avancées. Il est évident que l’énergie de production du bambou est de loin inférieure à celle de l’acier voire du béton. Cependant, le facteur confinement est déterminant. En effet, ce tableau se base sur l’utilisation de cannes de bambou. Or, c’est la fabrication de panneaux et planchers qui représente en volume la plus importante exploitation du bambou. Et l’énergie nécessaire à leur fabrication est naturellement bien plus importante que pour la production d’une simple canne.
Propriétés mécaniques
Le bambou, au même titre que le bois, est composé de cellulose, lignine et hémicellulose. Les celluloses sont la principale source de propriétés mécaniques du bambou et du bois. Sa structure moléculaire est définie par trois plans perpendiculaires. Le premier est constitué de nombreuses et fortes liaisons hydrogènes, le second par de plus faibles forces « Van der Waals » et le troisième par des liens covalents. L’observation de cette structure explique l’anisotropie du comportement de ce matériau. La résistance à la traction de la cellulose est évaluée à 8000 N/mm2.
Le chaume est constitué de 55% de cellules de stockage, de 35% de fibres pour la résistance, de 10% de tissus conducteurs d'eau et de sucre. Le pourcentage de fibres est plus élevé dans les parties extérieures et inférieures du chaume. En voici une coupe transversale (fig. 4).
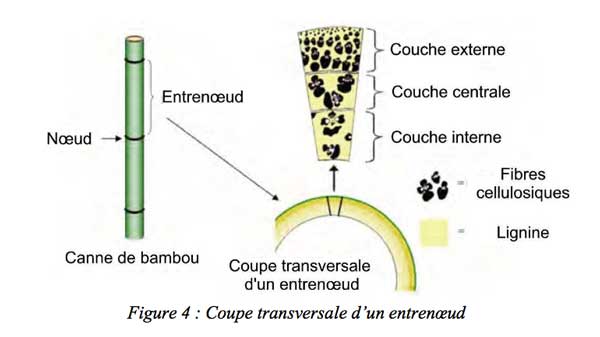
Dans la couche externe du chaume, les vaisseaux sont plus petits et plus denses. Vers l'intérieur, ils sont plus gros et moins nombreux. Les tissus et les cellules vasculaires sont concentrés à l'intérieur tandis qu'à l'extérieur les fibres assurent la résistance. Ces dernières représentent 60 à 70% du poids des tissus.
Dans les entrenœuds, les faisceaux vasculaires sont axiaux, verticaux et parallèles entre eux. La plupart des faisceaux traverse directement les nœuds pour rejoindre les entrenœuds suivants. L’étude microscopique des nœuds révèle un caractère anatomiquement différent. En effet, certains paquets de vasculaires dévient de leur trajectoire à hauteur du nœud. Les uns dans la zone extérieure, se rassemblent et se lient à ceux de la branche. Les autres, dans la zone intérieure, se lient à ceux du diaphragme (fig. 5).
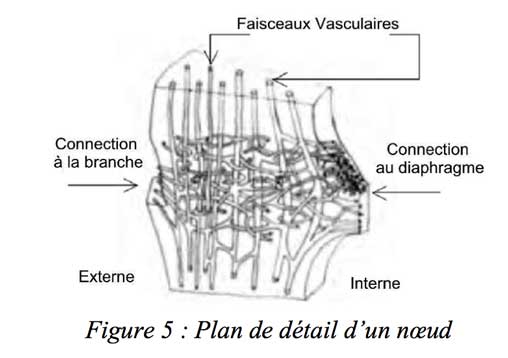
Le nœud est le paramètre qui influe le plus sur les propriétés physiques et mécaniques du chaume. Des études sur les nœuds du bambou ont montré que bien qu’ayant une densité plus élevée que celle des entrenœuds, ils sont nettement moins performants au point de vue de leurs propriétés mécaniques. Cette contre performance serait causée par la présence de fibres plus courtes et de faisceaux vasculaires tordus.
Comme pour le bois, les propriétés physiques et mécaniques du bambou changent considérablement entre les différentes espèces mais aussi entre différents chaumes d’une même espèce.
Vu la grande variabilité du comportement mécanique, les caractéristiques sont classées sous forme d’extremum et de moyenne (tab. 2) du bambou en comparaison avec le bois. Ces valeurs ne prennent pas en considération le bambou vert, fraîchement coupé.
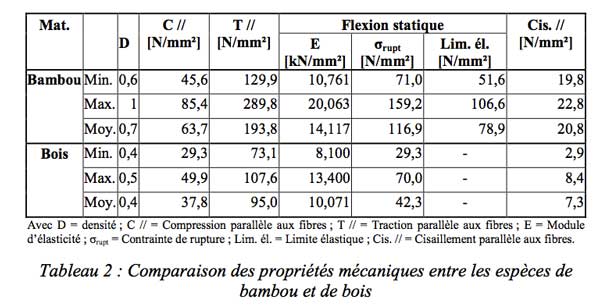
On retiendra que les performances mécaniques du bambou sont en général largement supérieures à celles du bois. Ceci confirme l’intérêt de ce matériau dans ce projet.
La densité du bambou explique aussi la dureté et durabilité particulièrement intéressante qui permet d’envisager des applications extérieures, pour palier les divers problèmes d’entretien connus pour le bois indigène.
Grâce aux nombreux avantages du bambou, mécaniques et autres, on compte en milliers les applications qui lui sont réservées. Son utilisation dans la construction permet des réalisations telles que maisons, supports de coffrage, couvertures de toiture, échafaudages, ponts, charpentes, armatures de béton, planchers et panneaux reconstitués.
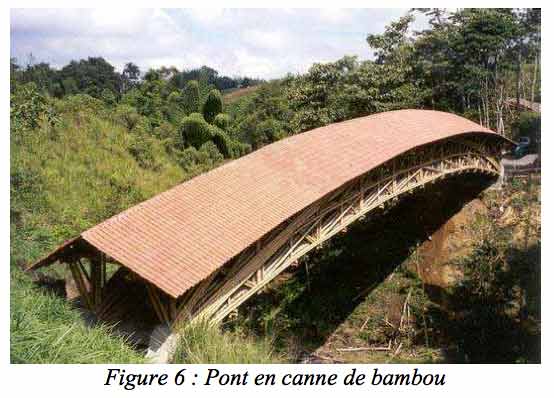
Fabrication de planchers et panneaux
L’idée de cette étude provient de la constatation qu’il n’existe que peu d’activités industrielles exploitant ce matériau. C’est loin d’être le cas pour la fabrication des planchers et panneaux en bambou qui connaissent actuellement un essor extraordinaire. C’est à partir de ce genre d’éléments que l’étude a été réalisée.
La fabrication des planchers et panneaux de bambou fait appel à un processus bien particulier. Contrairement au bois, les dimensions des lamelles ne dépassent pas 20-25 mm de large, 10 mm d’épaisseur et environ 2,5 m de long. Aussi, fut-il nécessaire d’adapter la technique à ces nouvelles données.
La première étape consiste à récolter la matière première. Les plantes forment d’innombrables « forêts de bambou». Après 3 à 5 ans, les cannes arrivent à maturité et leur diamètre, longueur et épaisseur permettent de réaliser les lamelles souhaitées. Ensuite, les plants sont simplement coupés à leur base et élagués.
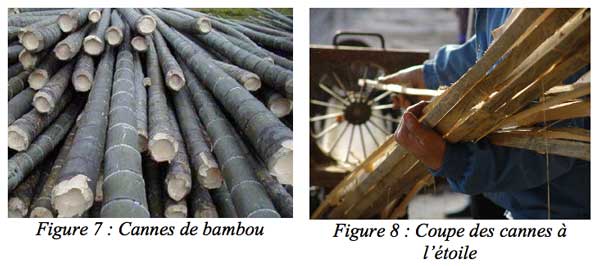
Une fois arrivées à la manufacture, les cannes sont coupées à longueur voulue et fendues, puis lamellées à l’aide d’un outil appelé étoile.
Les lamelles sont ensuite assemblées en fagots et stockées à l’abri de l’humidité afin de sécher endéans les trois jours après la coupe.
Chaque lamelle subit un calibrage quatre faces. La peau extérieure de la lamelle est alors retranchée ainsi que la matière peu fibreuse du côté intérieur de l’autre face. Ensuite, ce sont les côtés qui sont rabotés pour laisser apparaître une section finale rectangulaire. Ce calibrage permet de standardiser les dimensions des lamelles et faciliter la suite des opérations.
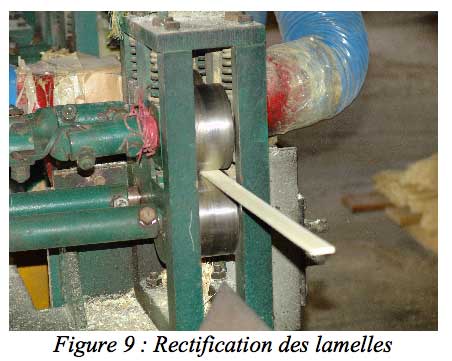
Le bambou est riche en amidon et sucre dont les insectes comme les mites sont friands. Une légère humidité fournirait un milieu propice pour la propagation de champignons.
Le traitement chimique emploie les préservatifs hydrosolubles tels que la formaline 0.5%, le sulfate de cuivre de Phénol+ 1 (1 de gamma : 2), chlorophénate 0.5% de penta de sodium et borax 1.5%. Les produits chimiques sont dissous dans l'eau. Les lamelles sont plongées dans ces solutions pendant 10 minutes.
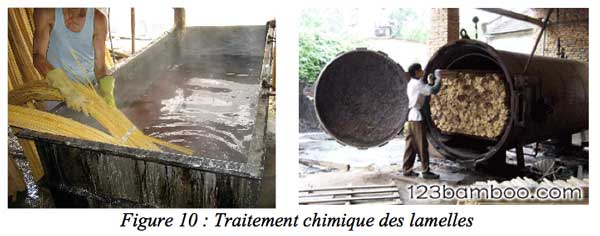
Un dernier traitement, accessoirement additionné au précédent est surtout utilisé pour la fabrication de planchers et panneaux. Il consiste à faire subir aux lattes un traitement thermique de vapeur d’eau à haute pression en autoclave. Aucun insecte ne résiste à ce traitement. Ce procédé permet aussi d’homogénéiser la couleur des lamelles.
Les lamelles sont ensuite séchées dans des fours à 70-80 °C pour être amenées à un taux d’humidité de 5 à 9 %, puis stockées dans des pièces tempérées. Ces étapes sont importantes pour garantir une bonne stabilité dimensionnelle.
La colle utilisée est l’urée formaldéhyde. La toxicité de ces colles est due aux émissions toxiques de formaldéhyde et de phényle, pouvant affecter le système nerveux. La norme européenne E1 limite les émissions à 3,5 mg/m2h. C’est de l’Aérolite UP4116, une poudre de résine à dissoudre dans l’eau, qui est utilisée pour les planchers. Le test selon EN 717-2 donne un résultat de 0,04 mg/m2h qui est largement inférieur à E1 et résiste aux tests mécaniques de haute adhérence de la norme américaine ANSI-3.
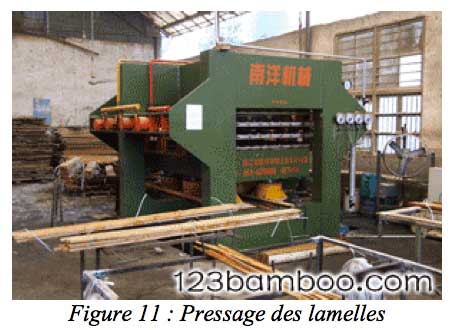
Avant d’être pressées, les lamelles sont collées et agencées de manière à former entre elles le matériau voulu. Le tout est alors mis sous presse automatique à une pression verticale de 10 kg/cm2 et 2,5 en pression latérale ou l’inverse en fonction du type d’élément. Le temps de serrage est compris entre 5 et 10 heures (fig. 11). Une fois les lamelles collées et pressées, elles sont poncées afin d’arriver aux tolérances dimensionnelles.
Dans le cas éventuel de la fabrication de poutres lamellé-collé, certaines étapes sont cependant facultatives.
Quatre types de produits lamellé-collé différents ont été utilisés au cours de l’étude. Les trois premiers se différencient par l’agencement des lamelles. Le quatrième met en jeu un procédé de fabrication quelque peu différent de celui exposé précédemment.
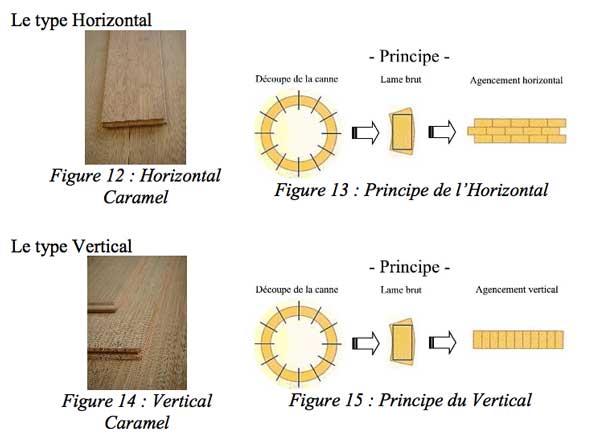
Le type Croisé, surtout utilisé lors de la fabrication de panneau afin de garantir la stabilité dimensionnelle dans les deux directions.
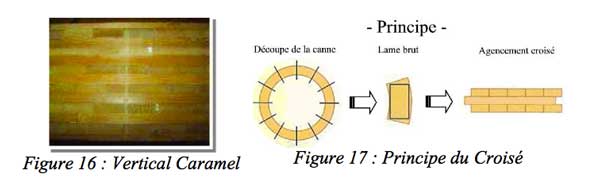
Enfin, le type BamWood est sans doute le matériau le plus intéressant et prometteur pour les applications envisagées par cette étude. Il se différencie principalement des autres par la manière même dont il est fabriqué. Les lamelles utilisées sont plus « brutes » et permettent de mieux valoriser la matière. Elles ne nécessitent pas de calibrage ni même l’arrangement contraignant des autres types. Elles sont empilées plus ou moins aléatoirement dans un moule en étant préalablement enduites de colle puis pressées sous très haute pression. Après la prise de la colle, l’ensemble peut être démoulé et se présente alors sous forme de gros blocs. Les blocs sont ensuite coupés en planches (fig. 18).
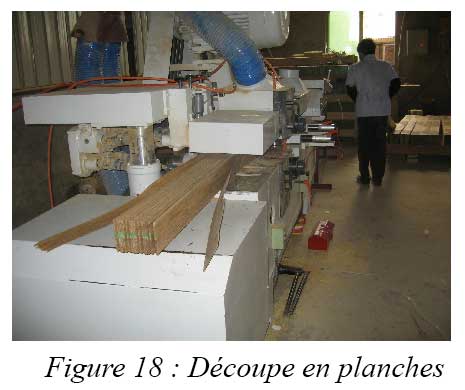
Mettons en évidence l’importance de la densité de fibres des lamelles. En effet, les fibres garantissent la reprise des contraintes appliquées sur le matériau. Dans ce projet de réalisation de poutres lamellé-collé, il est primordial d’accorder une attention particulière à ce paramètre. De lui dépendent les performances des poutres.
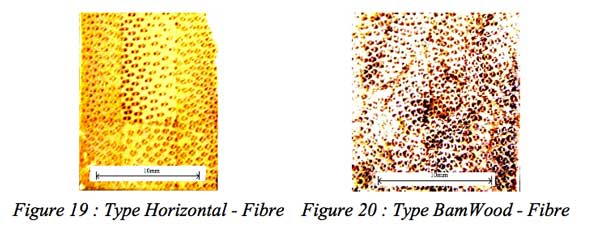
La dispersion des fibres au sein de la section du type Horizontal se voit de façon plus marquée que dans le type BamWood qui d’une part a plus d’homogénéité et d’autre part a une densité sensiblement plus importante.
Nous avons des coupes histologiques (fig. 21) effectuées par le CRNFB (Centre de Recherche Forêt Nature et Bois à Gembloux) dans une planche de type BamWood. On y voit clairement les différents joints entre les lamelles de section variable. On peut observer aussi l’homogénéité de la dispersion des faisceaux vasculaires.
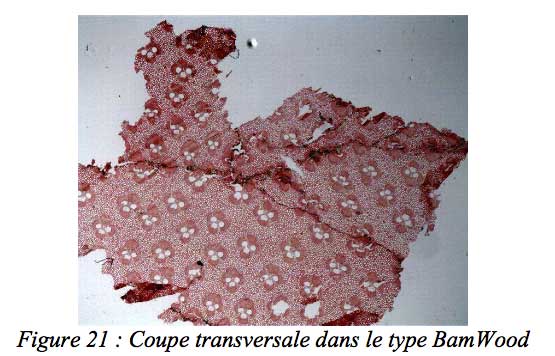
Articles annexes :
- Le bambou par wikipédia : http://fr.wikipedia.org/wiki/Bambou
- Fiche technique :
Bambou : http://www.acbois.fr/files/Fiche_technique_Bambou.pdf
Chène : http://www.acbois.fr/files/Fiche_technique_chene.pdf
Laurent